在塑料加工、橡膠制造及食品化工等眾多工業領域中,雙螺桿擠出機作為核心設備,扮演著將原材料轉化為具有特定形狀和性能產品的關鍵角色。而其中,它作為直接接觸并處理物料的部件,其設計與性能對產品的質量和生產效率有著直接影響。本文旨在深入探討雙螺桿擠出機螺紋套的結構特性、材料選擇、加工工藝以及其在實際應用中的表現,為相關領域的技術人員和研究人員提供有價值的參考。
一、結構特性:精密設計與功能實現
雙螺桿擠出機螺紋套,通常由多個螺紋元件組合而成,這些元件按照特定的排列順序裝配在芯軸上,形成連續的螺旋通道。它的設計需考慮物料流動的均勻性、剪切力分布、停留時間控制等多個因素,以確保物料在擠出過程中能夠充分塑化、混合并達到所需的物理化學性能。每個螺紋元件的形狀、尺寸、螺距以及相互之間的組合方式,都是根據具體加工需求精心設計的。例如,某些區域可能采用深槽設計以增加剪切力,促進物料混合;而另一些區域則可能采用淺槽或平滑設計,以減少不必要的熱量產生,保護物料特性。
二、材料選擇:耐磨與耐高溫的雙重考驗
鑒于它在工作過程中需要承受高溫、高壓以及高速旋轉帶來的強烈摩擦,其材料選擇至關重要。常見的材料包括硬質合金、工具鋼、不銹鋼以及某些特殊合金材料。這些材料不僅具有優異的耐磨性,能夠在長期使用中保持較低的磨損率,還具備良好的耐高溫性能,確保在高溫環境下仍能保持穩定的機械性能和尺寸精度。此外,針對特定加工需求,如腐蝕性環境或特殊物料處理,設備表面還會進行特殊的涂層處理或熱處理,以進一步提高其耐腐蝕性和使用壽命。
三、加工工藝:精密制造與質量控制
螺紋套的加工工藝涉及多道復雜工序,包括切割、磨削、熱處理、表面處理等。每一道工序都需要高度的、嚴格的質量控制,以確保它的尺寸精度、形狀精度和表面質量滿足設計要求。特別是螺紋的加工,往往需要采用高精度的數控機床或專用設備,通過編程和切削參數控制,實現螺紋的成型。此外,熱處理過程也是關鍵一環,它直接影響到設備的硬度、韌性和耐磨性。通過合理的熱處理工藝,可以在保證材料強度的同時,獲得較佳的綜合機械性能。
四、實際應用:效率與質量的雙重提升
在實際應用中,雙螺桿擠出機螺紋套的性能直接影響到生產效率和產品質量。優質的設計能夠優化物料流動路徑,減少死角和積料現象,提高物料的均質性和塑化效果。同時,合理的剪切力分布和停留時間控制,有助于改善物料的物理性能和加工穩定性。此外,它的易維護性和可更換性也是設計時需要考慮的重要因素之一。通過模塊化設計和快速更換機制,可以大大降低停機時間和維修成本,提高生產線的整體運行效率。
雙螺桿擠出機螺紋套作為擠出過程中的核心部件之一,其設計、材料選擇、加工工藝以及實際應用表現都直接關系到整個生產線的效率和產品質量。隨著科技的進步和工業的發展,對設備的性能要求也越來越高。未來,通過不斷的技術創新和優化設計,相信它將在更多領域發揮更加重要的作用。
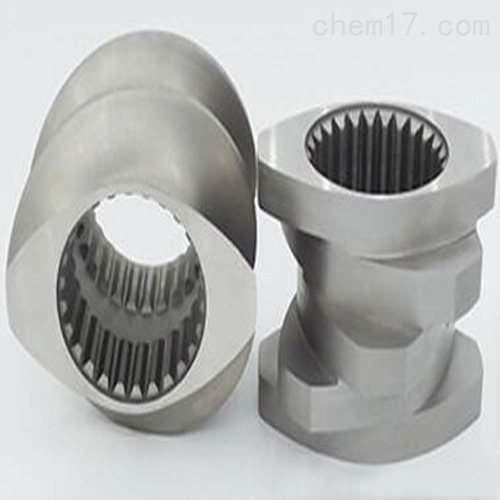